Click to read more about Contact Lens Manual: A Comprehensive Study and Reference Guide (Volume 1) by Executive Editor Joseph W. LibraryThing is a.
- South American Journal of Medicine, Volume-1, Issue-1, 2013 CASE REPORT - ANIRIDIA LENS WITH MANUAL SUTURELESS MEDIUM INCISION CATARACT SURGERY – BIG SIZE, BIG SURPRISE A Case Study by Dr.Jasdeep Singh Sandhu, India (M.S. Ophthalmology, PG Up-gradation Student of Texila American University) Email: sandhujasdeepsingh@yahoo.co.in ABSTRACT.
- (2) contact lens shall submit verification of completion of the Contact Lens Manual: Volume 1, A Comprehensive Study and Reference Guide, sponsored by the Contact Lens Society of America. (b) A registered apprentice applying for a dispensing optician license to dispense.
A technical overview of the development,manufacturing, and future of contact lenses
Justin Bergin
CE435
Introduction to Polymers
Department of Chemical Engineering
State University of New York at Buffalo
April 6, 2000
Abstract
Contact lenses are a modern technological breakthrough yet they have been in development for over 500 years.While the most important advances have come in the latter half of the 1900's, this area of science is still undergoing tremendous growth.Chemical engineer's are critical for the development and manufacturing of the contact lens of the future.This paper will attempt to give a brief overview of contact lenses.It will discuss the history, manufacturing, and science behind modern contact lenses.The paper will conclude by showing some of the tradeoffs of contact use, for no invention is without its drawbacks.
The History of Contact lenses
This first concepts of contact lenses were developed by Leonardo DaVinci in the year 1508.He drew sketches and depicted several forms of possible lenses.In 1632, Rene Descartes suggested the idea of the corneal contact lens, and in 1827 Sir John F. W. Herschel suggested that a glass lens could protect the eye from infection.1 These ideas were taken advantage of in the late 1800's by Adolph Fick, Eugene Kale, and August Miller.Working independently, these scientists created the first corneoscleral shell contact lenses.1,2,3The lenses consisted of blown glass, and were molded from rabbit and cadaver eyes.These glass lenses were relatively successful at protecting the eye from infected eyelids, and they showed promise at correcting vision as well.Initial lens designs covered the whole eye, including the white portion.While visual correction was attained to a certain degree, they were hard to make and very uncomfortable.Often times it took patients several months to be fitted correctly.The lenses were also very thick and heavy.The thickness gave the eye and unnatural appearance, and the pressure from the weight of the lenses caused discomfort and damage to the eye.1It was reported that in some cases the lenses was so painful, that cocaine anesthetic was used.2
The next major development occurred in the year 1936 when William Feinbloom, an American Optometrist, fabricated the first plastic contact lens.In 1948, Kevin Tuohey then designed the first designed the first corneal contact lens from poly (methyl methacrylate) also known as PMMA.This went on to become what is known as the hard contact lens.Hard Contact lenses became available commercially in 1979.These lens designs worked well and improved models of them are still sold today. 2
During this time Otto Wichterle discovered poly(hydroxyethyl methacrylate), (HEMA), and in 1961 he created the worlds first soft lens. HEMA is a hydrogel that could be made into contacts using a simply and efficient spin cast method.Since different corrections could be made by simple varying the spin rate and mould optic, this became a very efficient method for manufacturing lenses.Bausch & Lomb eventually attained the patients, and the FDA gave approved for HEMA based contact lenses to be used for daily wear in 1971.While HEMA was discovered after PMMA, it was the first contact lens to be approved by the FDA. 1, 2
In the years since polymers introduction, contact lens technology has been increasing at a rapid rate.There have been improvements in manufacturing techniques, as well as an increase in the type of polymer used in the lens.Manufacturing techniques moved from the lenses being hand made and polished, to modern day lathes where the lenses are cut with lasers to computer precision.While all contact lenses consist of amorphous chain linked polymers, the type of monomer used can significantly change the property of the lens.This push in technology was fueled by the desire for extended wear lenses, increased permeability, comfort, and biocompatibility.
How Contact Lenses Work
To understand the technological advances in the contact lens industry it becomes necessary to have an understanding of how contact lenses work, and their desired.A soft contact lens molds to the shape of the eye covering both the cornea and limbus.This is possible because the lens is soft and flexible.The lens floats in the layer of tear that is present on top of the eye.The eyelid and attraction between the polymer and tear film hold the lens in place.4
Hard contact lenses are not flexible, and this means that they must be ground to precisely fit the eye. They only cover the cornea, and not the limbus.If hard contacts are not fit precisely to the eye they will move and not work correctly.They are held in place by precise fitting and their attraction to the tear film. 4
Figure 1:How Contact Lenses Work
Picture courtesy of Scientific American @ http://www.sciam.com/2000/1000issue/1000working.html
Hard and soft contacts work similarly in that as light is refracted as it passes through the polymer.By varying the thickness and the shape of the lens the amount of refraction can be varied to produce different amounts of visual correction.
Why Do People Wear Contact Lenses
Contact lenses can be worn for multiple reasons.The majority of contact lens users wear them for vision to correct myopia, and some research has shown that contacts slow of the progression of myopia.In addition, contact lenses can also be worn to change the color of the eye for aesthetic reasons.The information in table one lists only a few of the conditions that favor contact lens use. 5
Table 1:Typical Reasons For Contact Lens Use5
What Makes a Good Contact Lens, and Biocompatibility
Several things must be considered when designing contact lenses, but perhaps the most important is biocompatibility.While several factors can affect a lenses biocompatibility, perhaps the most important is the wetability of the lens.Contact lenses are constantly in contact with the fluid of the eye. When the contact is placed in the eye, a layer of tear separated it from the eye.This is commonly known as the tear film.The human tear consists not only of water, but also of protein, lipids, sodium, calcium, bicarbonate, and enzymes. 6
If a polymer is hydrophobic it will repel the water that makes up a majority of the tear surface.This disrupts the tear flow, and results in the deposition of an albumin film on the lens.This reduces the effectiveness of the contact, and can cause infection and/or irritation.14This is due to the contact lens hindering the tear film that covers the eye. Therefore, if a contact lens surface is highly hydrophobic it must treated to be made hydrophilic.Doping the polymer or treating the surface of the polymer can do this change in the morphology of the surface. 2
Wetability is not the only reason for deposits on contact lenses.Most contact lenses consist of monomers and cross-link materials that have charges on the monomers.This charge distribution results in the attraction of proteins.This is because proteins also have charge distributions, and they attract one another.Protein or lipid depositions create a biofilm in the lens.This can result in the lens losing its ocular properties, and the turns turning a yellow color. The yellow color is a result of lens spoilage, a result of the diffusion of proteins and lipid into the lens. The push for extended wear lenses is limited by the lenses biocompatibility. 2, 7, 8For extended wear, the contact lens must be highly hydrophilic and must resist the deposition of a biofilm on the lens.
While the surface must resist the formation of a biofilm it must also be semi-permeable.The human eye does not receive adequate blood flow to supply the eye with enough oxygen, or to remove enough carbon dioxide.The eye relies on its exposure to the air for aid.If the contact lens does not provide adequate permeability, the eye suffers serious health effects. 2, 9,10, 11,12, 13This permeability, DK, is typically measured in units of Barrers (10-10 cm3 O2 (STP) cm/cm2s cmHg).24Where D is the diffusion coefficient, and K is the solubility coefficient.14 For a contact lens to be acceptable for extended wear they must have a DK of 100 Barrers. 2, 24The actual amount of oxygen reaching the cornea is called the oxygen transmissibility.This is in terns of DK/L, where L is the thickness of the lens.It can be seem that the amount of oxygen reaching the eye is inversely proportional to the lens thickness, L.14
While the polymer that makes up the lens is important it is also important, for it to be produced in a way so that there is no contamination to the eye.This means not only that that polymer itself is capable of being in contact with the eye, but also that it can be produced in a way so that any residual monomer or solution does not pose a health risk.It is important to test the monomers for biocompatibility, and to assure that the monomers used in the lens are highly pure.
In addition to the biochemistry of the lens, it must also be physically acceptable.A big requirement of the lens is that it must be lightweight.This allows it to be placed on the eye comfortably for extended periods of time without causing ocular strain.This is difficult because the lens must also be strong to avoid tearing and/or scratching, have a reasonably high modulus of elasticity for ease of handling, and yet still soft and flexible enough to feel comfortable on the eye.
The size and specific gravity of the lens also become important factors for eye comfort.If the lens is too thick it will interfere with the eyelid and cause discomfort.If the specific weight of the lens is significantly different from that of tears the lens will have a tendency to move up or down.This makes the lens unstable on the cornea, and makes fitting problematic. 14
Finally a good contact lens must be affordable.It has to be able to be made cheaply and efficiently so that it can be purchased at a reasonable cost.
Manufacturing of Contact Lenses
There are three primary ways in which contact lenses are manufactured.The first method of manufacturing is referred to at lathe cutting.In this method, the monomer is bulk polymerized into rods.The rods are then cut into buttons, which are placed in the lathe.The lathe is then guided by computer to cut the button into a lens.This method has a high yield, and moderate quality. 4
Figure 2: Schematic of Lathes
Picture courtesy of Scientific American @ http://www.sciam.com/2000/1000issue/1000working.html
Figure 3: Modern precision Lathes, and polishing machines for hard contacts
Pictures courtesy of C & H Contact Lens, Inc.@ Http://www.chcontacts.com/smrtmach.htm
The second method of forming contacts is referred to as spin casting.In this method, the liquid monomer is placed in a mold, the mold is then rotated. The monomer is then polymerized inside the rotating mold.This method produces a low yield, but high quality lenses.Spin Casting is good because the lens optics can be varied by simply varying the speed of rotation, and/or the shape of the mold. 14, 2
Figure 4: Spin Cast Mold
The final method for producing contacts is by cast molding.In this method the monomer is placed into a mold, the mold is then cast, and the monomer is polymerized.The lens parameters are varied by changing the shape of the anterior and posterior molds.This method produces high yield, and high quality lenses.It is the most popular form of manufacting.4
Figure 5: Cast Mold
Picture courtesy of Scientific American @ http://www.sciam.com/2000/1000issue/1000working.html
Hard Contact Lenses
Currently fifteen percent of the thirty million contact lens users wear what is known as hard contact lenses. 4 There are several kinds of hard contact lenses, the most historic being impermeable hard contact lens, and now the most common are the rigid gas permeable (RGP) lens, and silicone acrylate based lenses.All of these lenses consist of an amorphous three dimensional polymer matrix (typically a MMA derivative) that is below its glass transition temperature.The lenses are typically very stiff and have a high modulus of elasticity.This gives them a high tear strength, and makes them very easy to handle.4
The impermeable contact lens was the first type of hard contact to be developed.It consists of PMMA only.The MMA monomer is polymerized via ultra-violet or infrared radiation in the presence of cross-linkers and initiators.The lenses were then made by the lath cutting manufacturing process. 2
PMMA is an ideal polymer to be used for hard contact lenses because it is cheap and easy to make.It is moderately hydrophobic, which also contributes to it repelling proteins effectively.It has a typical oxygen permeability of 0.5 DK, which makes it effectively an impermeable membrane to oxygen and carbon dioxide.This impermeability is what restricts PMMA lenses from being used more then about 8 hours at a time.2, 23
This restriction has caused tremendous research in the area in hard contact lens permeability.It is possible to make theoretical calculations with respect to contact lenses by applying a modified version of Henry's law, and Fick's Law.The modified version of Henry's law for polymers below their glass transition temperature can be simplified as followed:
C = KDp + CH(bp/1+ bp)
C = KDp + CHbp(bp << 1)
C = (KD + CHb)p
C = K'Dp
Table 2: Units for Henry's Law for Polymers Below Their Glass Transition Temperature15,16
Fick's law for glassy polymers is given as:
N = -DD (dCD/dx) – DH (dCH/dx)
This can be simplified as follows:
N = -D'D(d/dx)(C D + CH)
N = -D'D (dC'/dx)
Table 3: Symbols used in Fick's for Glassy Polymers15, 17
These equations yield results that are reasonable, and that are in good agreement when applied to hard contact lenses.To gain the necessary data however one must know the free volume fraction of the polymer. 15, 16, 17Diffusion is heavily dependent upon the free volume because it is a measure of the polymers porosity.One possible way of finding this is by positron annihilation spectroscopy.This paper will not discuss this in depth, but more can be found in the references. 15
Research in the 1970's found that the impermeability of PMMA lenses could be overcome by copolymerizing MMA with silicone acrylate.A scientist by the name Norman Gaylord copolymerised methacryloxypropyl tris(trimethysiloxy silane), (TRIS),with MMA.The result was a polymer that had the strength of MMA, but also the oxygen permeability of silicone.Silicone is hydrophobic however, so the wetting agent methacrylic acid (MAA) was added to increase lens wetability.The PMMA-TRIS lens was the first RPG lens and was highly successful. Several lenses received FDA approval for daily wear, and are still used today. 2
Figure 5:Methacrylic Acid
PMMA-TRIS lenses were problematic because TRIS is hydrophobic, and lipophilic.In addition, the lenses still did not have the permeability's required for extended wear.This caused many complications in the push to develop extended wear lenses, and increase biocompatibility.Looking for a solution, researchers began looking into doping MMA-TRIS lenses with Fluoromethacrylates. 23Recent research has shown that doping lenses with Fluoromethacrylates increases the free volume fraction. 2,15Increasing the free volume fraction is like adding lanes to the diffusion expressway.It gives oxygen and carbon dioxide more room to penetrate the lens.Thus, it efficiently increases the polymers permeability, hence increasing comfort and decreasing ocular strain. 15This increase in the polymers permeability along with varying the thickness of the lens created a RGP lenses that were approved for extended wear for up to seven days. 2
While hard contacts are not the most the most convenient they are very cost effective.They are polymerized in bulk, and then cut with a precision lathe.This allows them to be made very cheaply.In addition, their relative impermeability makes then very resistant to environment of the eye.They typically repel proteins and lipids very effectively.With proper maintenance the lenses can be used for several years.Hard lenses are also very durable, and their strength helps them resist scratching, and protect the cornea. 2
Soft Contact Lenses
The most popular type of contact lens is a soft lens.Soft contact lenses are made of thermo-set polymer hydrogels.Like hard contacts lens polymers, these gels are made up of a three dimensional, amorphous network with cross-links.The lenses are soft because the polymer is above its glass transition temperature.Soft contacts are typically formed using cast molding or the spin cast method.They can be produced by the lath cutting process, but this is less common.23
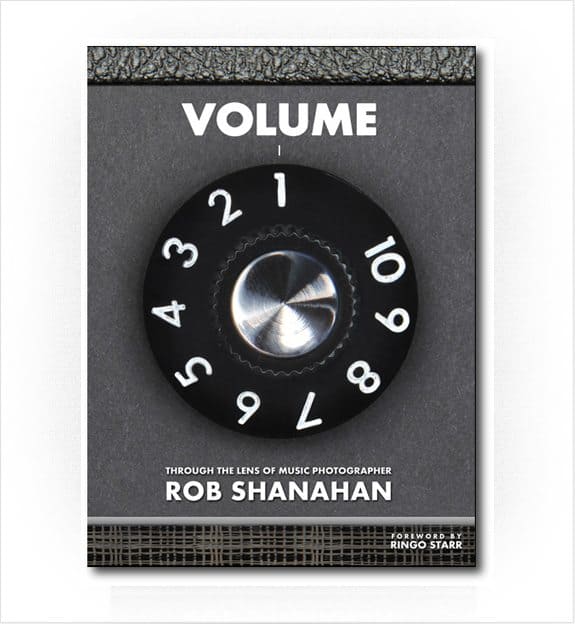
In soft contact lenses the water content affect many things. The permeability of the lens is proportional to the amount of water in the lens.As the percent weight of water increases in the lens, the permeability increases relatively linearly.The lenses ability to absorb various amounts of water also makes them highly hydrophilic. These attributes gives soft contact lenses the ability to achieve permeability's that allows them to be used for extended wear without damage to the eye.The increased permeability does not come freely however.As the water content is increased the polymers loose their strength.This can lead to tearing or scratching of the lens.A softer lens also offers the cornea less protection. 2
The first hydrogel contacts consisted of HEMA that was cross-linked with either ethylene dimethacrylate (EDMA) or ethylene glycol monogethacrylate (EGDMA).Future models of hydrogel lenses added the surfactants, methacrylic acid (MAA) and N vinyl pyrollidone (NVP) to increase water content.MMA is undesirable however because it makes the polymer ionic, which attracts proteins. 2,8,18HEMA has also been substituted with such monomers as glycerol methacrylate (GMA) that shows a higher resistance biofilm formation.Typical HEMA/MAA soft contact lenses have oxygen permeabilties of about 15-25 Barrers.2, 23
Figure6:Ethylene glycol monogethacrylate
Figure 8:Hydroxyethyl Methacrylate, and N Vinyl Pyrollidone
Seeking to improve soft contact lens permeability scientist started to make hydrogels from silicone based polymers like polydimethylsiloxane (PDMS)..The silicone hydrogel contact lens, also known as siloxane lenses, show impressive permeability (PDMS has a DK of 600 Barres), while retaining the comfort, wetability, and biofilm resistance of non-silicon based hydrogels.24 Unlike hydrogel lenses however, the oxygen permeability of silicone hydrogels decreases exponentially as water content increases.As discussed in hard contact lenses, silicone is hydrophobic, so the wetablity decreases as water content decreases. This led scientist to researching ways of making siloxane based lenses more wetable. 2, 19
The use of fluorine doped side chains has also become increasingly popular as a method to further increase permeability.When coupled with siloxane, fluorine can effectively increase the permeability while also effectively resisting lipid deposits.The challenge scientist encounter with fluorine is that it repels water.This leads them to cap fluorine chains with methacrylate with is less hydrophobic.25
The surface chemistry of soft contact lenses is of great importance.While the soft contact lenses typically have acceptable diffusion rates, all methacrylic and acrylic hydrogels are hydrophobic to a certain extent.In fact, it has been shown that while the water content of a hydrogel helps its permeability, it not little or nothing to affect its wetability.21In the case of siloxane lenses it is because the surfaces tend to consist of siloxane.Siloxane migrates to the surface of the lens during polymerization because of its desire of air.While siloxane is successful at repelling proteins, but it is highly hydrophobic which results in lipid and protein deposition on the lens.19Initial research attempted to blend hydrophobic silicone based monomers with hydrophilic monomers.These attempts were unsuccessful however because the difference in hydrophilicity would cause phase seperation. 2, 20 Recently with it has been shown that by grafting polyoxyethylene to the surface, the lens effectively repels protein and lipids, and increased wetability.Improved surfactants consisting of random copolymers of lauryl-, hexyl-, and methyl-methacrylate and polyethylene glycol methacrylate, have also shown a lot of promise.19The surfactants are bound to the surface during the actual making of the lens.The surfactant monomers are added to the contact lens monomers, and the surfactants moved to the surface during lens the creation of the lens because they have a higher desire for air then siloxane.Covalent bonds are then formed as the silicones of the gel matrix appear.19Currently silicone hydrogel lenses have DK's have about 50-200 Barrers, however none of these lenses currently in commercially availble.2
Attempts to improve the wetability of soft contact lenses have also been make on the manufacturing side of processing.Research has shown that by polymerizing the contact in polar molds effectively increased the wetability of the lens.This is because the charge distribution on the mold attracts charges to the surface of the lens while it is forming.Once the charges are at the surface of the lens, they are polymerized, and consequently forced to stay at the surface.24
The water in tears is then attracted to this polar surface of the lens.
Problems Caused by Contact Lens Use
The biocompatibility of contact lenses is at the forefront of scientific and engineering research.This is in partly due to the push for an extended wear lens, and also due to health disorders that arise from contact lens use.While many advances have been made in the biocompatibility, and physical properties of lenses, significant problems still exist.Possible contact lens disorders are listed in table.These disorders must be taken into account when comparing contact lenses to eye glasses or laser correction surgery.While taking out and removing contacts on a daily or weekly basis can be stressful, the eye can typically heal from contact lens disorders.This should be compared to laser surgery where a mistake can be fatally hazardous to the eye.The debate between contacts and laser surgery will increase in the future as laser surgery becomes more successful and contact lens manufacturers develop cheaper, 30 day extended wear lenses that have little risk of infection.
Table 4:Some Common Contact lens Disorders14,22
Conclusion
All contact lenses consist of amorphous, three-dimensional, polymer matrixes.Hard contacts consist of polymers that are below their glass transition temperature, and typically contain little or no water.Soft contact lenses consist of polymers that are above their glass transition temperature, and typically have a relatively high water content.
Hard Contact lenses have increased their permeability by thinning the lens, and doping MMA with TRIS and/or fluorine based monomers.Soft contact lenses have sought to increase their permeability in different ways.Hydrogel lenses has sought to increase water content, while siloxane hydrogels have tried to find ways of decreasing their water content.Some examples of the
Contact lens science has increased rapidly in the 20th century.While significant progress has been made, the most challenging aspect await to be solved in the 21st century.As we begin the new millennium polymer scientist are working in collaboration with biologist, chemist, and medical doctors to produce the extended wear lens.This lens will be able to be used for up to thirty days without removal, and be almost completely resistive to biofilm deposition.
References
1. Salvatori, P.L. The story of contact lenses.Obrig Laboratories: New York,
1960.pg. 19-24.
2. Kunzler, J.F. McGee, J.A. Contact Lens Materials Chemistry in Britian
3. Heitz, R.F. ‘Contact Lenses'. (2nd Edition, Volume 1) Dabazies, O.H. Little
Brown and Company, 1989.1.1-1.9.
4. Lubick, N. ‘The Hard and the Soft.' Scientific American. 10/2000
http://www.sciam.com/2000/1000issue/working.html
5. Hamano, H., Kaufman, H.E. The Physiology of the Cornea and Contact Lens
Applications.Churchill Livingstone: New York, 1987.Pages 69-74.
6. Larke, J. The Eye in Contact Lens Wear.Butterworths:Toronto, 1985. Page 24-27, 40-47.
7 Friends, G., Kunzler, J., Ozark, R., J. Biomedical Materials Research, 1992, 26, 59-67
8 ‘Biomedical Materials'.Juniper, R., Read, P.London: Elsevier, Novermber 1994,2
9.Holden, B., Mertz, G. McNally, J., Invest. Ophthalmol. Vis. Sci., 1983, 24, 218-22
10. Holden, B., Mertz, G., ibid, 1984, 25, 1161-7
11.Schoessler, J., International Contact Lens Clinic, 1983, 10, 148-51
12. Sarver, M., Baggett, D., harris, M. Louie, K., Am. J. Optom. & Physiol. Optics, 1981, 58, 386-
92
13.White, P., Contact Lens Spectrum, February 1990, 46-63
14.Rao, J.B., Saini, J.S. 'Complications of Contant Lenses.' Contact Lenses.
Aquavella, J. V., Rao, G. N.Lippincott Company. Philidelphia, 1987.pg. 48, 49, 71, 76-
77,195-225.
15. Singh, J. J., et. Al. 'An Investigation of Microstructural Characteristics of Contact-Lens
Polymers' NASA Technical Paper, 3034. December 1990.
16. Paul, D. R. 'Gas Sorption and Transport in Glassy Polymers.' Ber. Bunsenges.Phys. Chem.,
vol. 83, no. 4, 1979, Pages 294-302.
17. Petropoulos, J. H. 'Qualitative Analysis of Gaseous Diffusion in Glassy Polymers.'J.
Polymer Sci.: Pt A-2, vol. 8, no. 10. October, 1970. Pages 1797-1801.
18. Lai, Y., Wilson, A., Zantos, S., ‘Contact lenses' in ‘Kirk-Othmer encylopedia of chemical
technology', Volume 7, John Wiley, 1993, 191-213.
19. Ammon, D. M., Castner, D. G., Ratner, B.D.'In-Situ Surface Modifications ofContact
LensPolymers.'Surface modifications of Polymeric Biomaterials.
Grobe, G. L., McGee, J. A., Valint, P. L.Plenum Press. New York, 1997.pg. 21-26.
20. Mueller, K.F., Kleiner, E.K., US Patent No. 4740553, 1998
Precision 1 Contact Lens
21. Holly, F. J.,Refojo, M. F. 'Water Wetability of Hydrogels' Hydrogels for
Medical and Related Applications.Andrade, J. D.American Chemical
Society.1976pg 252-256.
22. Slatt B. J., Stein, H.A., Stein, R.M. Fitting Guide For Rigid and Soft Contact
Lenses.A Pratical Approach (3rd edition).C. V. Mosby Company, Toronto1990. pg. xvii-
Contact Lens Manual Volume 1 Answers
xxiv, 477-488
23.Bennett E. S.'Material Selection.' Clinical Manual of Contact Lenses.
Bennett, E. S.,Henry V. A.J. B. Lippincott Company Philidelphia,1994. pg.
27-40, 143-170, 197-217.
24. Friends. G. D., Lai, Y.C. 'Surface Wettability Enhancement of Silicone Hydrogel Lenses by
Processing with Polar Plastic Molds.'J. Biomed. Mater. Res., 35, 349-356, 1997.
25. Kunzler, J., Ozark, R. 'Methacrylate-Capped Fluoro Side Chain Siloxanes:Synthesis,
Characterization, and Their Use in the Design of Oxygen-Permeable Hydrogels.'J Appl
Contact Lens Manual Volume 1
Polym Sci. 65: 1081-1089, 1997.